Truck Wheel Bearing Replacement: When to Service 18-Wheeler Hubs
Truck Wheel Bearing Replacement: When to Service 18-Wheeler Hubs
Blog Article
Ensuring optimal truck performance isn't complicated. It's all about regular maintenance checks, spotting issues before they worsen, tracking fleet health, and implementing preventive approaches. Regular checks and fixes guarantee optimal uptime, improved productivity, and security. Expert guidance from experts like Jim can help you master fleet maintenance through the effective use of technology, detailed documentation, and qualified staff. Start exploring the ultimate guide to fleet maintenance and open the door to efficient operations. There's plenty to website learn and uncover!
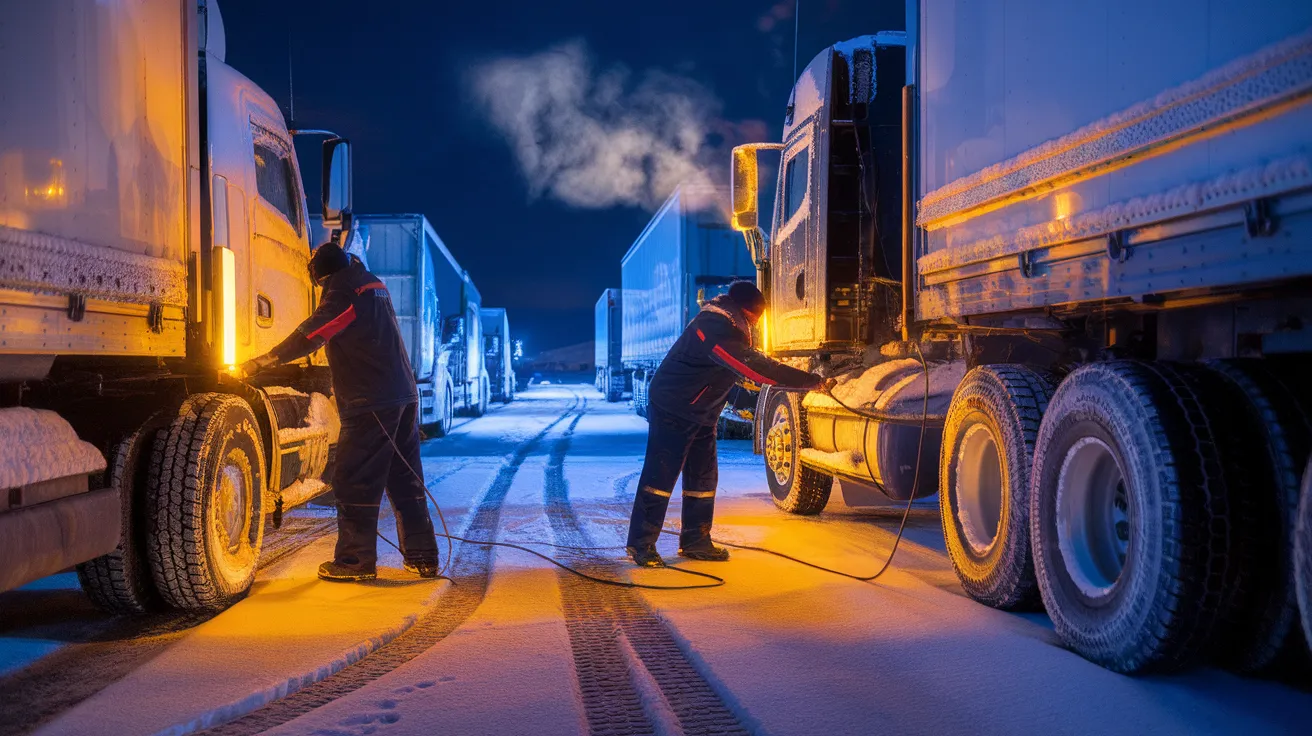
Core Concepts
Recognizing the Critical Role of Regular Truck and Fleet Maintenance
While it may appear challenging, understanding regular truck and fleet maintenance is crucial for every prosperous company. You'll find the advantages of maintenance far outweigh the resources you put in. Routine inspections and maintenance can substantially prolong the lifespan of your vehicles, avoiding hefty replacement costs. Moreover, there's an obvious relationship between well-maintained trucks and enhanced fuel performance. This means lower fuel costs, improving your total operational efficiency. Additionally, frequent maintenance can help identify minor issues before they develop into major issues, avoiding expensive repair bills down the line. So, don't overlook the value of routine maintenance; it can be a true difference-maker for your operation's success.
Examining Fundamental Parts of a High-Performance Maintenance Strategy
To secure your fleet's performance and lifespan, it's crucial to pinpoint the vital elements of a successful maintenance program. You'll need to understand the basic principles of maintenance, track the health of your fleet consistently, and establish preventive measures in advance. With these established, you're well on your way to reducing downtime and maximizing productivity.
Key System Maintenance Features
If you're looking to improve your fleet's productivity and longevity, implementing a robust maintenance program is vital. Critical elements of the program consist of scheduled inspections, routine servicing, and anticipatory repairs. Every component is instrumental in minimizing major malfunctions and limiting downtime. While the benefits of a maintenance program are significant, it's important to address the setup hurdles. These may include resource constraints and employee pushback. However, with proper planning, transparent dialogue, and focus on skill development, these barriers can be addressed. Keep in mind that an successful maintenance program goes beyond fixing problems; it prevents them. It's an commitment in your fleet's success – and it's one that pays dividends.
Equipment Status Tracking
As you delve into the fundamentals of a effective maintenance program, acknowledging the critical role of fleet condition monitoring is essential. It's not just about keeping your vehicles running, it focuses on optimizing fleet performance. Vehicle tracking solutions offer a complete view of your fleet's condition, allowing you to detect potential issues prior to escalation.
These monitoring systems track key metrics like fuel consumption, tire health, engine performance, and more. By leveraging this data, you're not only ensuring the longevity of your fleet but also minimizing unplanned repair expenses. Remember proactive identification is crucial in fleet management. Thus, invest in dependable monitoring technologies and remain ahead of the curve. Avoid simply responding to problems, forecast them. Keep your fleet's condition in check and your operation will operate efficiently.
Establishing Preventive Protocols
While monitoring your fleet's condition plays a vital role, implementing preventive measures is equally important to maintain a robust maintenance program. You must spot potential concerns before they develop into costly repairs or downtime. Let's explore preventive maintenance approaches.
A key strategy is developing a thorough maintenance checklist. This list should outline all necessary inspections, maintenance procedures, and parts renewal. Routine engine inspections, tire rotations, and oil changes are fundamental. However, remember to check basic components like windshield wipers, lights, and filtration systems.
Your maintenance plan needs to include a timetable for every maintenance item. Adhering to this timeline ensures that your fleet maintains optimal performance. Remember, preventive measures reduces expenses, time, and problems in the long run.
Essential Routine Checks for Transport Fleet Care
To guarantee your fleet and trucks remain in optimal condition, you must emphasize regular maintenance inspections. These checks encompass regular service evaluations and critical component assessments. By following these vital routines, you'll maximize your fleet's longevity, optimize operational efficiency, and in the end, minimize costly repairs.
Planned System Examinations
Regular maintenance inspections represent your strongest line of defense from unplanned vehicle and fleet malfunctions. They provide you a chance to detect and fix concerns before they turn into costly repairs or dangerous accidents. One of the most significant benefits of routine maintenance is the prevention of downtime, which can substantially influence your business's efficiency and profitability.
Key Component Evaluations
Following up on the importance of scheduled maintenance inspections, let's move towards the specific essential component checks that must be conducted regularly to maintain maximum truck and fleet performance. First examine the brake system – confirm all components are working properly, from brake pads to fluid levels, as well as checking for leaks. Neglected, brakes may malfunction, leading to serious incidents. Monitoring tire pressure is equally crucial. Underinflation raises fuel consumption and tire wear, while excessive pressure can cause a blowout. Invest in a reliable pressure gauge for accurate readings. Note that tires should be cold during checks for best results. Consistently conducting these critical checks can save you from costly repairs and potential accidents. Maintain safety on the road.
Essential Fleet Maintenance Practices for Peak Performance
In fleet management, it's crucial that you focus on preventative maintenance to ensure peak efficiency. Implementing a well-structured preventative scheduling system is essential. This minimizes unnecessary wear and tear, and lowers the chances of unscheduled downtime. You should schedule regular inspections and maintenance based on engine hours, mileage, time, or fuel usage. Note that each vehicle is unique and could require a personalized approach.
Maintenance training is a crucial approach to maintain peak efficiency. Equip your team with the essential skills to detect potential issues early on. This not only saves time but also reduces costs. The combination of preventative scheduling and maintenance training will create a highly effective and reliable fleet. Remember, an ounce of prevention is worth a pound of cure.
Crucial Pointers for Commercial Vehicle Upkeep and Renovation
Although truck and fleet repair and restoration can seem overwhelming, knowing the basics can help simplify things. Your starting point needs to be to understand various repair techniques. This understanding will help you identify issues effectively and promptly. Following this, prioritize maintenance work according to the severity of damage and the vehicle's role within your fleet. Frequently check all units for possible problems and tackle them quickly to stop issues from worsening. Don't forget, maintenance isn't only about repairs, it's focused on enhancing the vehicle's functionality and longevity. Finally, consistently choose premium components for maintenance; they'll provide better durability and performance. Follow these principles, and you'll manage truck and fleet repair and restoration successfully.
Harnessing Industry Innovations for Advanced Fleet Operations
To remain competitive in the trucking industry, it's vital to harness innovative solutions for advanced fleet maintenance. Technological advancements are rapidly changing the maintenance landscape. Implement data analytics to monitor your fleet's performance and identify problems before they occur.
State-of-the-art monitoring systems keep track of engine conditions and status, fuel usage, and driver behavior patterns. Utilize these insights to implement predictive maintenance, helping reduce costly operational interruptions.
Always prioritize software updates. These updates typically include critical updates and fixes that boost your automotive fleet's performance and safety. Note that fleet management isn't limited to routine maintenance. You're managing in a tech-focused era, and staying current with sector developments will support your fleet's sustainability and success. By implementing appropriate procedures, you can lower costs and time, and safeguard human life.
Questions & Answers
What Skills Should a Professional Vehicle Fleet Mechanic?
You will require an official certification, meeting the standards of an accredited mechanic institution. Moreover, you require a comprehensive skill assessment, proving your knowledge in various aspects of fleet repair and maintenance. Experience counts too!
What's the Right Time to Replace Fleet Vehicle Tires?
Just like the seasonal changes, you should regularly check your fleet's tread depth on a consistent basis. Nevertheless, experts suggest to install new tires every 3 to 6 years, according to driving conditions and frequency of use.
What Are the Warning Signs of Truck Engine Problems?
You'll spot engine trouble in trucks by indicators including unusual engine noise and poor fuel performance. Additional indicators are unusual exhaust smoke, fluid leakage, or possibly a continuously lit check engine warning.
What Role Does Technology Have in Modern Truck and Fleet Maintenance?
Technology is crucial in optimizing truck maintenance. Telemetry systems deliver real-time data, while analytical tools forecast issues before they happen. You'll experience less vehicle downtime, better safety measures and in the end, reduced expenses. It's transformative.
What Maintenance Considerations Apply to Different Types of Fleet Vehicles?
Each type of vehicle demands specific maintenance schedules. One must account for the vehicle's function, load capacity, and driving conditions, as these aspects substantially impact the necessary maintenance. Be sure to customize maintenance according to the type of vehicle.
Final Thoughts
Ultimately, the key is keeping your fleet running smoothly, right? Consistent upkeep isn't optional, it's a must. By identifying key components, performing regular inspections, using preventative strategies, and harnessing industry innovations, you're not just maintaining your trucks, you're developing a high-performance fleet. And keep in mind, fleet servicing isn't a problem, it's an opportunity for restoration. Stay committed, and you'll see your fleet's efficiency, reliability, and longevity achieve new levels.
Report this page